Durability of Light Steel Frame (LSF) Structures in Varied Humidity Conditions
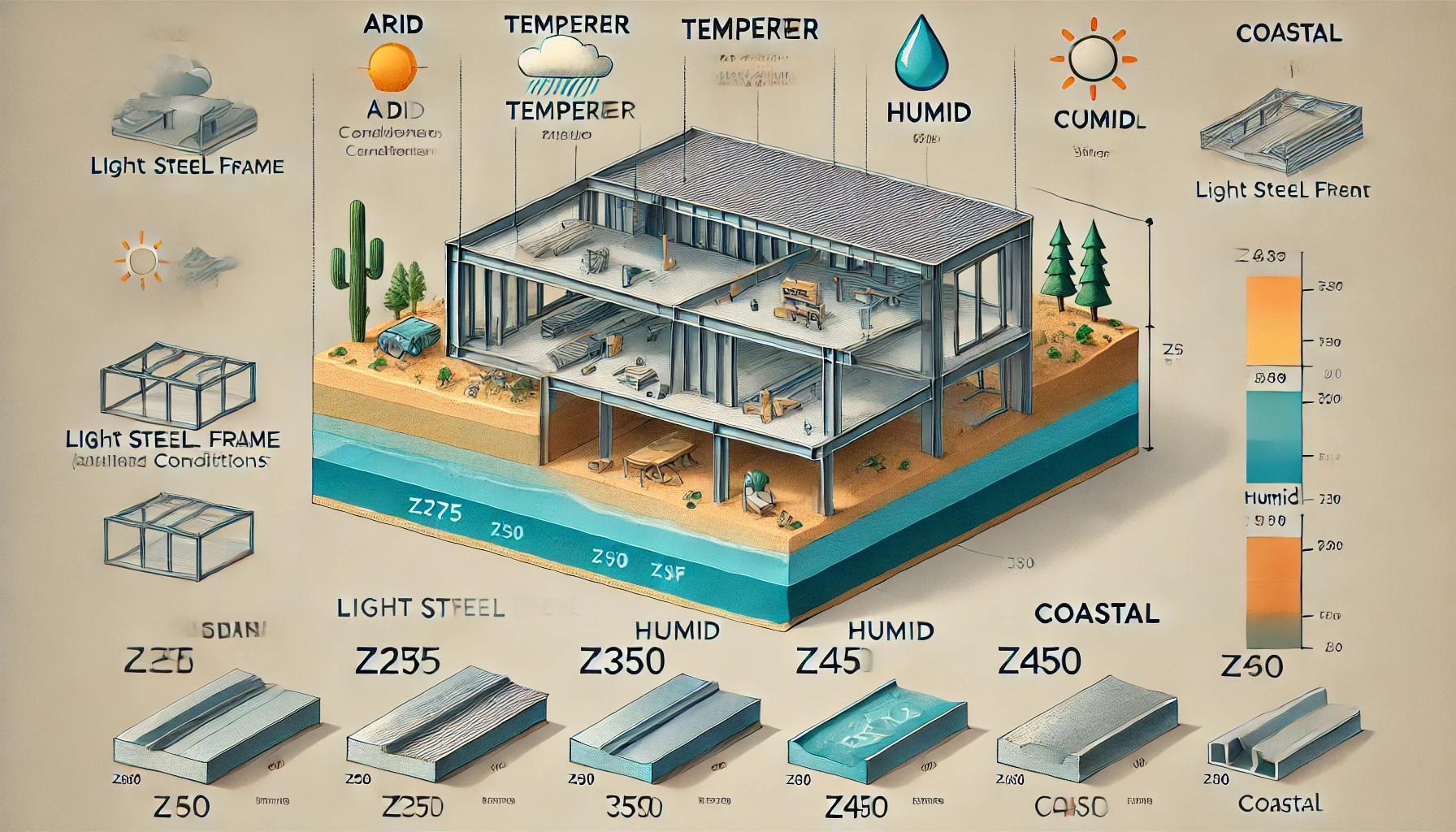
In construction, especially in light steel frame (LSF) structures, galvanized steel sheets play a crucial role due to their corrosion resistance and durability. Here’s an overview of types, coating requirements, and relevant standards for galvanized steel sheets commonly used in construction:
Types of Galvanized Steel Sheets
1. Hot-Dip Galvanized (HDG):** The most common type, where steel is dipped in molten zinc to form a robust zinc coating. This method provides excellent protection against corrosion, making it suitable for LSF and other structural applications.
2. Electro-Galvanized (EG):** In this method, zinc is applied using electroplating, resulting in a thinner zinc coating. Electro-galvanized sheets have a smoother surface finish than HDG but offer less corrosion protection, often used in indoor applications or environments with lower humidity.
3. Galvannealed (GA):** This is a process similar to hot-dip galvanizing but involves heating the sheet after the zinc coating to create an iron-zinc alloy layer. Galvannealed sheets are highly resistant to corrosion and are easier to paint, making them ideal for applications where additional finishes are needed.
Coating Thickness and Coating Class
The zinc coating on galvanized steel sheets is measured by weight or thickness and is often specified in terms of “g/m²” (grams per square meter) or in microns. The amount of coating affects the durability and corrosion resistance.
Typical coating classes for LSF structures are:
- Z120 - Z275: (or equivalent in microns) Common for construction, where Z275 provides more robust corrosion resistance with 275 g/m² of zinc coating on both sides.
- Z350 and above: Recommended for more demanding environmental conditions, providing higher corrosion resistance.
The thickness of the coating generally ranges from 12 to 25 microns for each side, depending on the application and the environmental exposure.
Standards and Specifications
Several international standards specify the requirements for galvanized steel sheets, including coating weight and methods:
- ASTM A653/A653M: Common in North America, specifying requirements for hot-dip galvanized steel.
- EN 10346: Used in Europe, covering continuous hot-dip coated steel sheet products.
- JIS G3302: Japanese standard for hot-dip galvanized steel sheets, specifying thickness, coating, and mechanical properties.
- ISO 3575 and ISO 4998: International standards for galvanized sheets used in construction.
For optimal performance, especially in LSF, sheets with coating class Z275 or higher are generally recommended to withstand outdoor exposure and extend the lifespan of the structure.
The lifespan of Light Steel Frame (LSF) structures made with galvanized steel is highly dependent on environmental factors, particularly humidity. Here’s how humidity affects the durability of LSF structures and some guidelines to maximize their lifespan based on environmental conditions:
Impact of Humidity on Galvanized Steel in LSF Structures
1. Low Humidity (Below 60%)
- lifespan: In environments with relatively low humidity, such as arid or semi-arid regions, galvanized steel LSF structures can last 50 years or more.
- Corrosion Rate: Lower humidity levels slow down the corrosion process, allowing the zinc coating to protect the steel for an extended period.
2. Moderate Humidity (60-80%)
- lifespan: In temperate regions with moderate humidity, the lifespan of LSF structures with standard zinc coatings (e.g., Z275) generally ranges from 30 to 50 years.
- Corrosion Rate: Moderate humidity levels increase corrosion but can still be managed with proper coating thickness. Regular inspections and maintenance can also help extend lifespan.
3. High Humidity (Above 80%)
- Lifespan: In highly humid environments, such as coastal or tropical areas, the lifespan of galvanized steel LSF structures may reduce to around 20-30 yes if exposed directly to high humidity or salty air.
- Corrosion Rate: High humidity accelerates the corrosion process, so thicker coatings (e.g., Z350 or higher) or additional protective layers are recommended.
4. Very High Humidity with Salt Exposure (e.g., Coastal Regions)
- Lifespan: In coastal areas with salty, humid air, the lifespan of standard galvanized steel LSF structures could be significantly shorter, around 15-25 years unless extra protective measures are taken.
- Corrosion Rate:*Salt accelerates the breakdown of zinc coatings, so using advanced corrosion-resistant coatings, such as Z450 or higher, and regular maintenance is crucial for durability.
Recommendations for Enhancing Durability
- Use Thicker Zinc Coatings:*For high-humidity or coastal environments, using a thicker zinc coating class (e.g., Z350 or Z450) is advisable.
- Apply Additional Coatings: In extreme cases, applying additional anti-corrosive paints or barrier layers over galvanized steel can further increase its resistance.
- Regular Maintenance and Inspections: Regularly inspect and maintain LSF structures to check for early signs of corrosion, especially in connections and joints where moisture can accumulate.
By carefully selecting the coating type and thickness and planning for maintenance, the lifespan of LSF structures in different humidity levels can be optimized, ensuring structural integrity and safety for the intended duration.