The Role of Self-Drilling Screws in Enhancing the Efficiency and Structural Integrity of Light Steel Frame (LSF) Construction
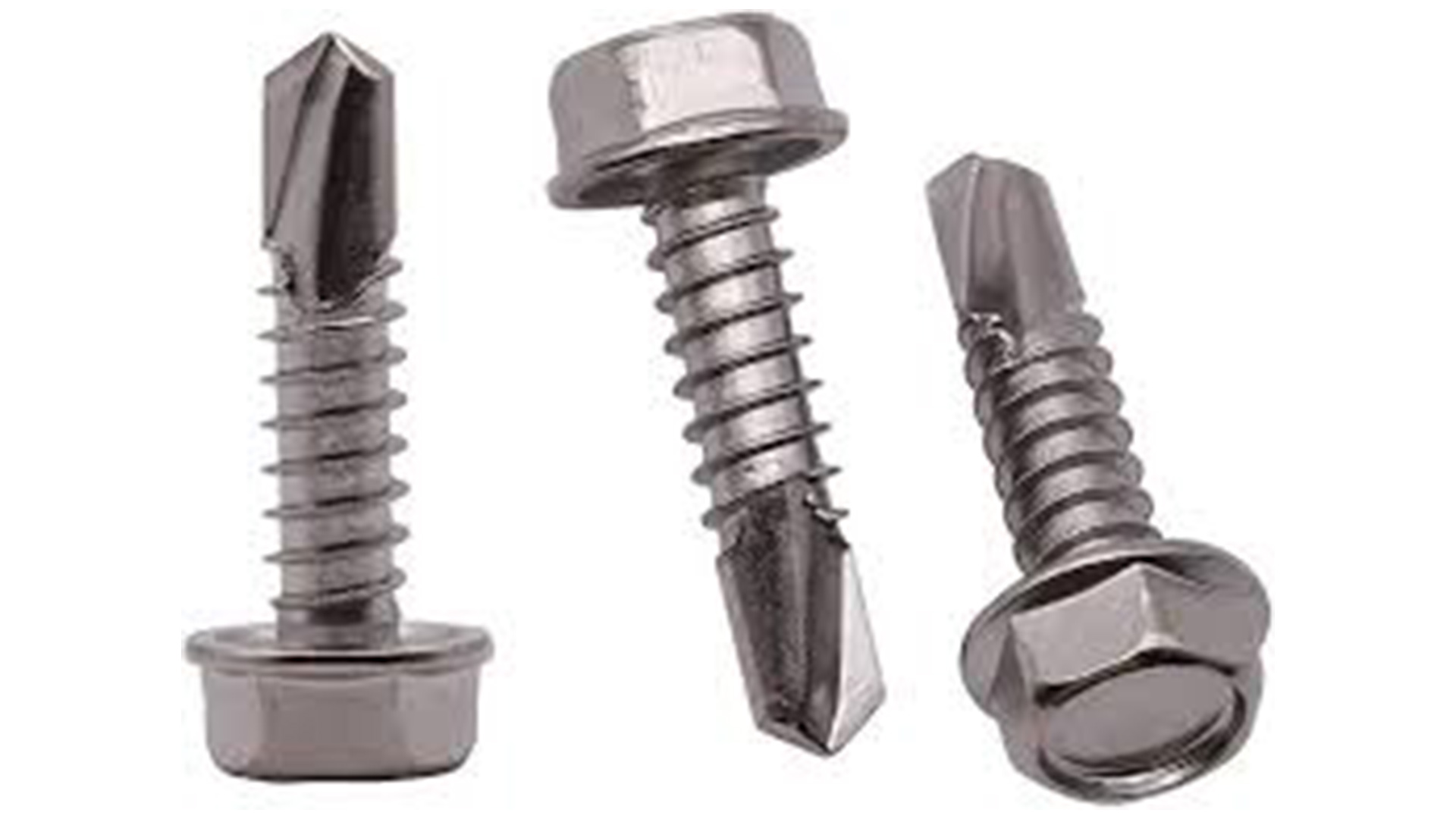
1.Introduction to Self-Drilling Screws for Light Steel Frame (LSF) Construction
Light Steel Frame (LSF) construction has emerged as a popular choice in modern building design due to its versatility, efficiency, and sustainability. This construction method relies heavily on the use of cold-formed steel sections, which are lightweight yet strong, making them ideal for a wide range of applications, from residential buildings to commercial and industrial projects. One of the critical components that ensure the stability and durability of LSF structures is the self-drilling screw.
Self-drilling screws, commonly referred to as Tek screws, are specifically designed to simplify the assembly of LSF structures. These screws combine the functions of drilling, tapping, and fastening into one operation, eliminating the need for pre-drilled holes. This feature not only speeds up the construction process but also ensures precise and consistent connections between the steel members.
The use of self-drilling screws in LSF construction offers several advantages:
- Ease of Installation: Self-drilling screws are designed with a sharp drill point that penetrates steel effortlessly, reducing the time and effort required for installation. This makes them highly suitable for projects where speed and efficiency are crucial.
- High Strength and Reliability: Made from high-strength materials and engineered for durability, these screws provide excellent pull-out and shear resistance. Their ability to create secure and robust connections ensures the structural integrity of LSF buildings.
- Versatility: Tek screws come in various sizes and types, allowing them to be used for different connections, such as wall-to-wall, stud-to-plate, and bracing. They are compatible with steel thicknesses ranging from light-gauge to thicker sections.
- Cost-Effectiveness: By combining multiple functions into a single screw and reducing installation time, self-drilling screws contribute to cost savings in labor and materials.
- Clean and Precise Connections: Unlike traditional methods, self-drilling screws minimize deformation and damage to the steel sections during installation, ensuring a clean and professional finish.
In this article, we will explore the types, properties, and applications of self-drilling screws in detail, highlighting their critical role in the success of LSF construction. By understanding the science and engineering behind these screws, engineers, builders, and architects can make informed decisions to optimize the performance and safety of their structures.
2.Types of Screws Used in LSF Structures
When constructing Light Steel Frame (LSF) structures, the choice of screws is crucial for ensuring the strength, stability, and longevity of the building. Self-drilling screws, commonly referred to as Tek screws, are the preferred fasteners for connecting the components of LSF structures. These screws eliminate the need for pre-drilling, saving time during installation and improving efficiency.
2.1 Tek Screws: Overview and Features
Self-drilling screws are designed with a drill bit at the tip, allowing them to penetrate steel sheets without pre-drilling a hole. This feature is particularly beneficial in LSF construction, where the steel components are often thin and precise connections are essential. The key components of a Tek screw include:
- Drill Point: This is the most distinctive feature of Tek screws. The drill point allows the screw to drill through the steel before the threads engage, making the installation process faster and more precise.
- Thread Design: The threads are designed to cut into the steel and create a strong bond. The number of threads varies depending on the size of the screw and the thickness of the steel being fastened.
- Head Style: Tek screws typically feature a hexagonal head that requires a wrench or socket for tightening, ensuring a secure and stable connection. The head style can vary, including flat, round, or pan types, depending on the application.
2.2 Types of Tek Screws
There are different types of Tek screws, each suitable for specific applications in LSF structures. The main types include:
- Tek 2 (Type 17) Screws: These screws are commonly used for lighter steel applications, typically up to 1.2 mm thickness. They are ideal for attaching thin steel components such as cladding or roofing sheets. Tek 2 screws have a sharp point that facilitates quick penetration into the steel.
- Tek 3 (Type 23) Screws: Designed for thicker steel components (ranging from 1.5 mm to 3 mm), Tek 3 screws have a larger drill point and are ideal for securing framing members or heavier panels in LSF structures. They provide a deeper engagement with the steel, enhancing the shear strength of the connection.
- Tek 4 (Type 25) Screws: These screws are used for the heaviest-duty applications and are capable of drilling through steel up to 6 mm thick. They are typically used for securing larger structural members, such as beams and columns, in LSF frameworks. Tek 4 screws offer superior pull-out and shear strength compared to Tek 2 and Tek 3 screws.
2.3 Selection Criteria for Tek Screws
The selection of the appropriate Tek screw for an LSF project depends on several factors:
- Steel Thickness: The thickness of the steel being fastened determines the type and size of the screw. For thinner steel (up to 1.2 mm), Tek 2 screws are sufficient, while thicker materials (1.5 mm to 3 mm) may require Tek 3 screws, and very thick steel (over 3 mm) necessitates Tek 4 screws.
- Load-Bearing Requirements: The intended use of the connection (whether it’s a load-bearing or non-load-bearing connection) also influences the screw selection. Screws used for high-load connections must have higher shear and pull-out strengths.
- Environmental Conditions: If the structure will be exposed to harsh weather conditions or corrosive environments, corrosion-resistant coatings (such as zinc plating or galvanization) may be required to protect the screws from degradation over time.
2.4 Common Applications of Tek Screws in LSF
Tek screws are used in a variety of applications within LSF construction, including:
- Wall-to-Wall Connections: Securing the vertical studs to horizontal tracks.
- Panel Assemblies: Attaching metal panels to framing members.
- Bracing and Reinforcements: Installing diagonal bracing or reinforcing members.
- Roofing and Cladding: Attaching roof panels and external cladding to structural frames.
Each type of screw is selected based on the load requirements, steel thickness, and environmental conditions of the specific application.
3. Mechanical Properties of Tek Screws
When selecting screws for Light Steel Frame (LSF) construction, understanding their mechanical properties is essential for ensuring structural integrity and performance. The two most critical mechanical properties of Tek screws are yield strength (Fy) and tensile strength (Fu). These properties directly influence the screw’s ability to hold connections together under load and during the life of the structure.
Yield Strength (Fy)
Yield strength refers to the maximum stress a material can withstand without permanent deformation. For Tek screws used in LSF systems, the yield strength is crucial because it determines how well the screw can maintain its shape and structural function under stress without yielding or bending. The typical yield strength of Tek screws used in LSF construction is 920 MPa (134 ksi). This means the screws can resist significant stresses before they start to deform, ensuring that the connections remain stable and functional throughout the structure’s lifespan.
Tensile Strength (Fu)
Tensile strength is the maximum stress a screw can endure while being pulled apart. It is a key factor for determining how much force the screw can resist before breaking. For Tek screws, the tensile strength is typically 1054 MPa (152 ksi). This high tensile strength allows the screws to withstand heavy pulling forces and ensures that they can hold connections firmly, even when subjected to fluctuating loads, such as wind or seismic forces.
Importance for LSF Construction
In LSF systems, screws act as the primary fastening mechanism for various structural components, including walls, studs, and braces. The combination of high yield strength and tensile strength in Tek screws allows for secure and reliable connections between these components. Furthermore, the mechanical properties of these screws ensure that they will not fail under normal operational loads, providing safety and stability to the entire structure.
Impact of Steel Thickness
The performance of Tek screws is also influenced by the thickness of the steel in which they are installed. For example, screws used in 1.2 mm thick steel will have slightly different load-bearing capabilities compared to screws used in thicker steel. The interaction between the screw threads and the steel material determines the screw's ability to resist both pull-out forces (when the screw is pulled out of the steel) and shear forces (when the screw is subjected to lateral stresses). Understanding the steel gauge and its impact on the screw's performance is vital for selecting the appropriate screw size and type for each specific LSF application.
By focusing on the mechanical properties of screws, engineers can select the best screws for each connection, ensuring the LSF structure is robust, safe, and durable over time.
4. Load-Bearing Capacities of Tek Screws
When selecting screws for Light Steel Frame (LSF) structures, understanding the load-bearing capacities is critical for ensuring the integrity and safety of the building. Tek screws, commonly used in LSF construction, must provide sufficient strength to withstand both pull-out and shear forces. These forces are fundamental to the performance of the connections between steel members, and the right screw size and type are essential for achieving optimal structural performance.
1. Pull-Out Strength
Pull-out strength refers to the resistance a screw provides against being pulled out of the steel material to which it is fastened. This is a key factor in determining the ability of screws to maintain the stability of connections, especially in structural elements that bear significant loads. Pull-out strength is influenced by various factors, including the screw size, the number of threads engaged, and the thickness and type of steel being used.
For LSF structures, the typical pull-out strength is measured in Newtons (N). The steel thickness significantly affects the screw's pull-out performance. For instance, a screw installed in 1.2 mm thick steel will exhibit lower pull-out strength compared to screws installed in thicker materials, as the engagement of the threads with the steel is more limited.
- Example: A #10-16 screw (4.8 mm diameter) driven into 1.2 mm steel typically achieves a pull-out force in the range of 1300 to 1800 N. For thicker steel, such as 2 mm, the pull-out strength may increase significantly, reaching 2000 N or higher.
The pull-out force can be further optimized by ensuring proper installation, such as using the right drill point (e.g., Tek 2 or Tek 3) and achieving the necessary thread engagement. It is important that the screw penetrates sufficiently into the steel and that the threads are not stripped or damaged during installation.
2. Shear Strength
Shear strength refers to the ability of the screw to resist forces that attempt to slide or shear the connected steel members apart. This is particularly relevant in connections where the screw is subjected to lateral forces or stresses, such as in bracing systems or load-bearing panels. Shear strength is typically measured in Newtons (N) or pounds (lbs) and depends on the screw size, material strength, and the way the screw is installed.
The shear capacity of a Tek screw increases with its diameter and length, as larger screws have more surface area to resist shear forces. In LSF construction, #12-14 or #14-14 screws (5.5 mm and 6.3 mm diameter, respectively) are often used for connections where higher shear resistance is required, such as in areas of the building that experience high dynamic loads or wind pressure.
- Example: A #12-14 screw (5.5 mm diameter) typically achieves a shear strength in the range of 2500 N to 3500 N when installed in 1.2 mm thick steel. This makes it suitable for structural connections like header-to-wall connections or for securing larger panels.
Factors Affecting Load-Bearing Capacities
Several factors affect the load-bearing capacities of screws, including:
- Screw Size: Larger screws offer higher pull-out and shear strengths due to their increased surface area and thread engagement.
- Steel Thickness: Thicker steel provides more material for the screw to engage with, leading to higher pull-out resistance.
- Material Type: The material properties of both the screw and the steel (e.g., tensile strength, hardness) influence how well the screw will hold up under load.
- Installation Quality: Proper installation is crucial. Screws must be installed at the correct angle and torque to ensure they perform as intended. Over-tightening can lead to thread stripping, while under-tightening can reduce the screw's holding capacity.
Pull-Out and Shear Strength of Tek Screws ( Metric Units)
5.Design Guidelines for LSF Connections
When designing Light Steel Frame (LSF) structures, selecting the right screws for connecting various components is essential for ensuring the strength and durability of the frame. Self-drilling Tek screws are commonly used for these applications, as they provide ease of installation and reliable performance. Here are key guidelines for selecting and using screws in LSF connections:
1. Selection of Screw Size and Type
- Screw Size: The size of the screw is determined by the thickness of the steel being used in the LSF structure. For instance, screws sized #8-18 (4.2 mm) are suitable for light-duty connections, while larger screws like #12-14 (5.5 mm) and #14-14 (6.3 mm) are used for more substantial connections where higher shear and pull-out resistance is required.
- Screw Type: Different screw types, such as Tek 2, Tek 3, and Tek 4, offer varying levels of thread engagement and drilling capability. For example:Tek 2 screws are ideal for thinner steel (up to 1.5 mm), while Tek 3 and Tek 4 screws are designed for thicker materials and provide deeper thread engagement, improving holding strength.
2. Thread Engagement
- The effectiveness of a screw in LSF construction largely depends on the number of threads engaged with the steel. For optimal performance, ensure that the screw engages at least 3 full threads within the steel material. This engagement provides the necessary pull-out resistance and shear capacity to hold the components together securely.
- For steel thicknesses above 1.2 mm, consider using screws with deeper threads to achieve better engagement and strength.
3. Connection Types
- Wall-to-Wall Connections: For connecting walls to other framing members, such as headers or corner posts, #10-16 or #12-14 screws are typically used, as these screws offer higher shear strength for structural stability.
- Stud-to-Plate Connections: In stud wall assemblies, screws like #10-16 provide adequate pull-out and shear resistance when fastening studs to the top and bottom plates. For heavier load-bearing applications, screws such as #12-14 are better suited.
- Bracing and Diagonal Members: For securing bracing elements or diagonal members, use #12-14 or #14-14 screws, which provide higher shear capacities needed for these high-stress areas.
- Double Steel Sheets: In situations where multiple layers of steel are joined (e.g., double steel sheets or reinforced panels), larger screws with greater penetration and holding strength, such as #14-14, may be necessary.
4. Screw Installation
- Correct Alignment: Ensure that screws are driven perpendicular to the surface of the steel to maximize thread engagement. Incorrect angle placement can weaken the connection, leading to reduced load-bearing capacities.
- Torque Control: Over-tightening screws can strip the threads or damage the steel, while under-tightening may result in inadequate thread engagement. It is essential to use a torque-limiting drill or impact driver to ensure the correct tension is applied.
- Pre-Drilled Holes: For some applications, it may be beneficial to pre-drill holes to guide the screws and reduce the risk of misalignment, particularly in thicker materials where self-drilling may become difficult.
5. Consideration of Environmental Factors
- Corrosion Resistance: Since LSF structures are often used in a variety of environments, including exterior applications, it is important to choose screws with adequate corrosion resistance. Zinc-plated screws or stainless steel screws are recommended for environments exposed to moisture or salt.
- Environmental Conditions: In coastal or industrial environments with high humidity or corrosive elements, it is advisable to use screws with special coatings, such as galvanized or weather-resistant finishes, to prolong the lifespan of the connections.
6. Load Calculation and Safety
- Proper load calculation is crucial for ensuring the screw’s performance under both static and dynamic loads. The screw should meet the required pull-out strength and shear strength based on the specific design loads. A comprehensive load analysis should be performed, accounting for both dead loads (permanent loads) and live loads (temporary or moving loads).
- Always refer to the manufacturer’s specifications for the exact performance of screws, as these values are tested and verified for different steel thicknesses and application scenarios.
6.Comparison of Screw Types for Specific Applications in LSF Structures
When selecting screws for Light Steel Frame (LSF) structures, it's essential to consider various factors, including the load-bearing requirements, the type of connection, and the thickness of the steel. Self-drilling screws, commonly known as Tek screws, come in different sizes and types, each suited for specific applications. Below, we will compare the most commonly used screw types for LSF structures based on their suitability for various applications.
1. Smaller Screws: #8-18 (4.2 mm)
Use Case:
- Light-duty applications: These screws are typically used for lighter connections where the load-bearing capacity is lower. Examples include securing wall panels to studs, connecting interior partitions, and attaching cladding to the frame.
- Ideal for thinner steel: Screws of this size work well with steel gauges from 1.0 mm to 1.5 mm thickness.
Advantages:
- Cost-effective: Smaller screws tend to be less expensive, making them ideal for budget-conscious projects.
- Easier to install: Due to their smaller size, they require less torque and can be installed quickly, especially in repetitive tasks.
Limitations:
Lower load-bearing capacity: While adequate for light connections, they are not suitable for high-stress areas or heavy-duty joints.
2. Medium-Sized Screws: #10-16 (4.8 mm)
Use Case:
- Standard LSF connections: These screws are widely used for structural applications such as securing studs, attaching horizontal and vertical bracing, and connecting framing members.
- Works well with medium steel thicknesses: These screws are ideal for steel thicknesses between 1.2 mm and 2.0 mm.
Advantages:
- Balanced load capacity: They offer a good balance between cost, ease of installation, and load-bearing capacity. These screws are perfect for the majority of LSF structural connections.
- Versatility: Their ability to securely fasten materials together while maintaining durability makes them a go-to choice for various types of joints.
Limitations:
Not suitable for heavy-duty applications: For areas subjected to high shear or pull-out forces, larger screws are recommended.
3. Larger Screws: #12-14 (5.5 mm)
Use Case:
- Heavy-duty connections: These screws are used in applications where higher strength is required, such as attaching heavy framing elements, securing roof trusses, or joining thicker steel members (typically 2.0 mm to 3.0 mm steel thickness).
- Ideal for structural frames: In buildings with larger spans or higher load demands, these screws provide enhanced pull-out and shear capacities.
Advantages:
- Higher load capacity: These screws are designed to handle more stress, making them ideal for areas where load distribution and strength are critical.
- Longer thread engagement: The larger size ensures better thread engagement, which improves pull-out resistance in thicker materials.
Limitations:
- More expensive: Larger screws are generally more costly, making them less suitable for less demanding parts of the structure.
- Requires more installation torque: The larger screw size demands higher torque for installation, which may slow down the process compared to smaller screws.
4. Heavy-Duty Screws: #14-14 (6.3 mm)
Use Case:
- High-strength connections: These screws are typically used for the most demanding applications, such as securing load-bearing walls, connecting structural steel elements, or attaching foundation elements where maximum strength and durability are necessary.
- Best for thick steel: They are most effective with steel thicknesses of 2.5 mm or greater, particularly in areas subject to high shear or tensile forces.
Advantages:
- Maximum strength: These screws provide superior shear and pull-out resistance, making them suitable for critical structural joints.
- Long-term reliability: Heavy-duty screws are ideal for areas exposed to harsh conditions or high stresses, ensuring the long-term integrity of the structure.
Limitations:
- High cost: The increased strength and durability come at a higher cost, which may make them less economical for large-scale projects where such strength is not needed.
- Installation complexity: The need for higher torque and precision during installation may increase the time and labor costs.
Summary of Recommendations:
- #8-18 screws are ideal for light-duty applications, such as securing cladding or interior panels to a frame.
- #10-16 screws are the most versatile and are suitable for a wide range of LSF connections, from studs to horizontal framing members.
- #12-14 screws should be used for heavier connections, where greater strength and higher load capacity are required, such as truss connections and thicker framing materials.
- #14-14 screws are best for high-strength, load-bearing joints, where maximum resistance to shear and pull-out forces is needed.
Choosing the correct screw size ensures the integrity and safety of the LSF structure, optimizing both performance and cost-effectiveness. For each specific application, the screw should be selected based on the required load-bearing capacity, steel thickness, and connection type.
7.Installation Best Practices for Tek Screws in LSF Structures
Proper installation of Tek screws is critical to ensuring the structural integrity and long-term performance of Light Steel Frame (LSF) structures. Even the strongest screws can fail if they are not installed correctly. Below are key best practices to follow during installation:
1. Select the Right Screw for the Job
Before installation, ensure that the chosen screw matches the thickness of the steel and the intended load requirements. For example:
- Use smaller screws (e.g., #8-18 or #10-16) for lighter connections like sheathing or bracing.
- Use larger screws (e.g., #12-14 or #14-14) for heavier loads, such as top plates or structural joints.
Always check the manufacturer’s specifications for pull-out and shear capacities to match the connection’s demand.
2. Use the Correct Installation Tool
Tek screws are designed to self-drill and self-tap, but the right tool is essential for smooth installation:
- Drill Type: Use a power drill with adjustable torque settings to prevent over-driving.
- Drive Socket: Ensure the socket size matches the screw head (e.g., 5/16" socket for most Tek screws).
- Speed Control: Use a moderate speed to avoid damaging the screw or steel surface.
3. Ensure Proper Alignment
For maximum performance:
- Install screws perpendicular (90 degrees) to the steel surface.
- Misaligned screws may not engage enough threads with the steel, reducing pull-out resistance and compromising the connection.
4. Maintain Minimum Edge Distance
Always maintain the recommended edge distance to avoid splitting or deforming the steel profile:
- Typically, keep screws at least 10 mm away from the edge of the steel member.
- For closer distances, verify with the screw manufacturer if additional measures are required.
5. Achieve Full Thread Engagement
The screw threads must fully engage with the steel for optimal pull-out strength:
- For a 1.2 mm steel thickness, ensure at least 3 full threads are embedded in the steel.
- Avoid over-drilling, which may strip the threads or reduce holding capacity.
6. Monitor Drill Point Performance
Tek screws come with drill points (e.g., Tek 2, Tek 3) designed for specific steel thicknesses:
- Use Tek 2 for thinner materials (up to 2 mm).
- Use Tek 3 or Tek 4 for thicker materials (2-5 mm). If the screw struggles to penetrate the steel, switch to a higher-capacity drill point.
7. Prevent Over-Tightening
Over-tightening screws can strip the threads or deform the steel profile, reducing both pull-out and shear resistance:
- Stop drilling as soon as the screw head is flush with the surface of the steel.
- Use torque-controlled drills to prevent over-driving.
8. Inspect Connections During and After Installation
Regular inspection ensures the quality of the connections:
- Look for properly seated screw heads without gaps or damage to the steel.
- Check that screws are fully engaged and not over-tightened or misaligned.
- Replace any improperly installed screws immediately to maintain the integrity of the structure.
9. Use Corrosion-Resistant Screws in Harsh Environments
In environments prone to moisture or corrosion, such as coastal areas, use screws with protective coatings:
- Zinc-coated or stainless steel screws are ideal for such conditions.
- Check for compliance with relevant corrosion resistance standards (e.g., ASTM B117).
10. Train Installers and Follow Manufacturer Guidelines
Finally, ensure that all personnel involved in the installation process are trained in proper techniques:
- Follow the screw manufacturer's recommendations for installation torque, edge distances, and pre-drilling (if required).
- Use checklists to standardize and monitor installation practices on-site.
8.Corrosion Resistance and Material Considerations for Tek Screws in LSF Structures
Corrosion resistance is a critical factor when selecting screws for Light Steel Frame (LSF) construction, as the longevity and structural integrity of the connections depend heavily on their ability to withstand environmental factors. Tek screws, commonly used in LSF systems, are available in various materials and coatings designed to resist corrosion and ensure durability in diverse conditions.
1. Importance of Corrosion Resistance in LSF Construction
- Environmental Exposure: LSF structures are often exposed to varying environmental conditions, such as humidity, rain, and temperature fluctuations. Corrosion can compromise the screw's structural performance, leading to weakened connections over time.
- Longevity: Properly coated or corrosion-resistant screws prevent degradation, ensuring the safety and durability of the structure throughout its service life.
- Aesthetic Considerations: Visible screws in exposed areas should remain free from rust to maintain the visual appeal of the structure.
2. Common Coatings and Materials for Corrosion Resistance
Several options are available for enhancing the corrosion resistance of Tek screws used in LSF construction:
- Zinc Plating: One of the most common coatings, zinc plating provides a protective layer that prevents the steel screw from direct exposure to moisture and air. Zinc-plated screws are suitable for general indoor use and mild outdoor environments.
- Galvanized Coating: Hot-dip galvanizing involves coating the screw with a thick layer of zinc, offering superior corrosion resistance compared to standard zinc plating. These screws are ideal for outdoor applications or regions with moderate exposure to moisture.
- Epoxy or Polymer Coatings: Advanced polymer or epoxy coatings provide an additional layer of protection against corrosive elements. These are particularly beneficial in coastal areas where structures are exposed to salt-laden air.
- Stainless Steel Screws: Stainless steel screws offer inherent corrosion resistance without requiring additional coatings. These are recommended for highly corrosive environments, such as marine or industrial settings, but may be more expensive than coated alternatives.
- Class 3 and Class 4 Coatings (AS/NZS 3566 Standard): These are specific grades of anti-corrosion coatings widely used in Australia and New Zealand. Class 4 is recommended for severe external environments, such as coastal areas.
3. Choosing the Right Screw for Your Project
When selecting screws for LSF projects, consider the following:
- Location and Climate: Coastal or industrial areas with high levels of salinity or pollutants require screws with advanced corrosion resistance, such as stainless steel or Class 4 coatings.
- Structure Usage: Indoor structures or components that are not exposed to moisture may only require zinc-plated screws.
- Project Budget: While high-performance screws with advanced coatings are more expensive, they can save costs in the long run by reducing maintenance and replacement needs.
4. Maintenance and Inspection
Even with corrosion-resistant screws, periodic inspections are essential, particularly in highly corrosive environments. Identifying early signs of corrosion allows for timely replacement and prevents further structural damage.
By carefully selecting the appropriate material and coating for Tek screws in LSF construction, designers and builders can ensure that their structures remain safe, durable, and visually appealing over time. Balancing cost considerations with the demands of the environment is key to achieving optimal performance and longevity.
9.Standards and Certifications for Tek Screws in LSF Construction
The use of Tek screws in Light Steel Frame (LSF) structures is subject to strict standards and certifications to ensure safety, durability, and compliance with building regulations. These standards govern the mechanical properties, performance, and suitability of screws for various structural applications. Below is an overview of the key standards and certifications relevant to Tek screws in LSF construction:
1. Mechanical Performance Standards
- ASTM Standards (American Society for Testing and Materials): Tek screws used in LSF construction often adhere to ASTM standards, such as:
- ISO Standards (International Organization for Standardization): ISO 15480 outlines the technical requirements for self-drilling screws, including dimensions, mechanical properties, and corrosion resistance.
2. Tensile and Shear Strength Testing
Tek screws must meet specific criteria for tensile and shear strength to be suitable for structural applications. For example:
- Yield Strength (Fy): Defined as the stress at which the screw deforms permanently, typically 920 MPa for high-performance screws.
- Tensile Strength (Fu): The maximum stress a screw can withstand before failure, often around 1054 MPa.
These values are verified through laboratory testing in accordance with standards such as ASTM E8 or ISO 6892 for tensile properties of materials.
3. Corrosion Resistance Standards
Since screws in LSF structures may be exposed to moisture or harsh environments, corrosion resistance is a critical factor:
- EN 12944-2: Defines the protective coatings required to prevent corrosion, such as galvanized or zinc-plated coatings.
- ASTM B117: Specifies the salt spray test used to evaluate corrosion resistance, simulating long-term exposure to corrosive environments.
4. Installation and Quality Assurance
Standards also ensure that screws are installed correctly and perform as intended:
- ANSI Standards: For self-drilling screws, ANSI/ASME B18.6.4 provides specifications for installation torque, thread engagement, and screw performance.
- CE Marking (Europe): Tek screws must carry CE certification to indicate compliance with European safety and quality standards.
5. Certification Bodies
Certifications from recognized organizations provide assurance of compliance with the above standards. Examples include:
- ICC-ES (International Code Council Evaluation Service): Issues reports verifying the suitability of screws for use in LSF structures.
- ETA (European Technical Assessment): Provides certifications for screws under the European Union's Construction Products Regulation (CPR).
6. Importance of Using Certified Screws
Using screws that meet industry standards is essential for:
- Ensuring the safety and stability of LSF structures.
- Complying with building codes and regulations.
- Preventing premature failures due to inadequate mechanical or corrosion resistance.
10.Case Studies: Application of Tek Screws in Real LSF Projects
Self-drilling Tek screws play an indispensable role in Light Steel Frame (LSF) construction, offering fast, reliable, and strong connections. To highlight their importance, this section presents real-world case studies where Tek screws have been successfully utilized in various LSF projects.
1. Residential Housing: Securing Wall-to-Wall Connections
In a residential housing project in Europe, #10-16 Tek screws were used to assemble walls and connect studs to tracks. The LSF structure was constructed using 1.2 mm thick galvanized steel profiles. The screws, with their sharp drill points, efficiently penetrated the steel without pre-drilling, reducing installation time by 30%.
- Challenges: Ensuring proper alignment of the studs during assembly.
- Solutions: The use of hex washer head (HWH) screws allowed easy positioning and minimized the risk of misalignment.
- Outcome: The structure was completed ahead of schedule, with joints demonstrating excellent pull-out and shear strength in post-construction testing.
2. Industrial Warehouses: Heavy-Duty Connections
In a large-scale industrial warehouse project, thicker steel profiles (2.0 mm) required the use of #14-14 Tek screws. These screws offered higher shear capacity, ideal for securing heavy bracing and roof trusses.
- Challenges: High wind loads demanded connections with superior strength.
- Solutions: High-tensile Tek screws with corrosion-resistant coating were selected, ensuring both strength and durability under harsh environmental conditions.
- Outcome: The warehouse structure withstood multiple stress tests, including simulated wind loading, demonstrating the reliability of the chosen screws.
3. Modular Schools: Rapid Assembly with Lightweight Materials
A modular school construction project prioritized quick assembly and lightweight materials. #8-18 Tek screws were used for connections between thin steel profiles (1.0 mm thickness). Their compact size and precision threading were ideal for minimizing material deformation during fastening.
- Challenges: Balancing lightweight design with structural stability.
- Solutions: The use of multiple screws per joint ensured sufficient load distribution without compromising the lightweight nature of the structure.
- Outcome: The school was erected within weeks, with its structural integrity meeting all safety and seismic standards.
4. A-Frame Buildings: Custom Design Applications
In an A-frame cabin project, LSF profiles with 1.5 mm thickness required screws capable of withstanding complex angled connections. #12-14 Tek screws with enhanced drill points were employed for angled joints between rafters and beams.
- Challenges: Achieving precise angled connections without compromising screw strength.
- Solutions: Using self-drilling screws with extended threads ensured secure connections even at steep angles.
- Outcome: The resulting structure showcased both aesthetic appeal and structural soundness, making it a showcase project for LSF construction versatility.