Choosing the Right Steel for LSF Structures: A Quick Guide
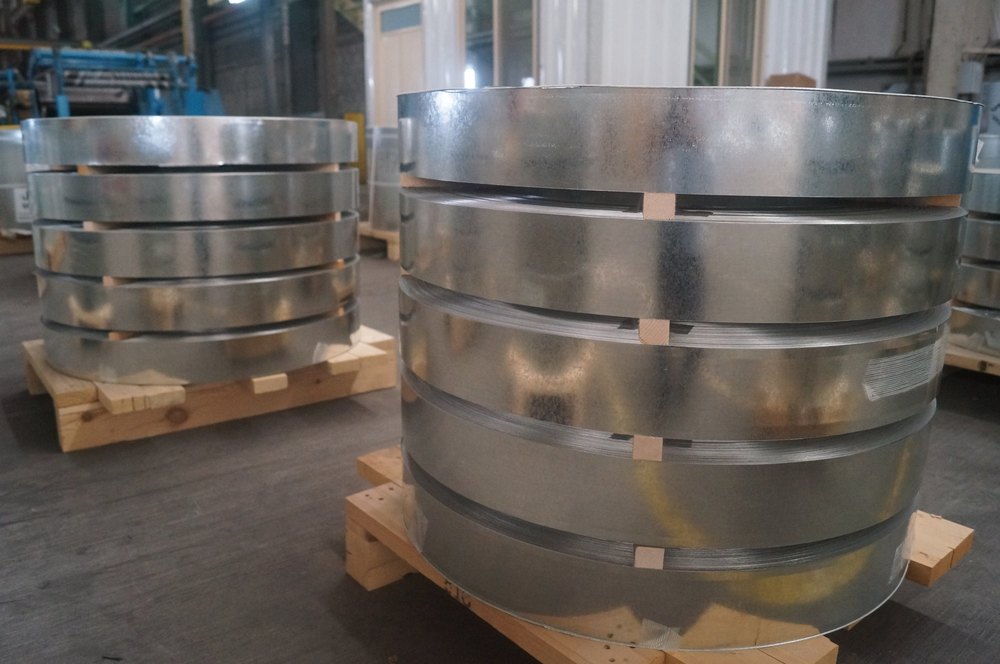
1- Introduction
Light Steel Frame (LSF) structures have gained popularity in modern construction due to their lightweight nature, ease of assembly, and versatility. These structures are widely used in residential, commercial, and industrial projects, offering an efficient alternative to traditional construction methods.
Selecting the right type of steel is one of the most critical decisions in LSF construction. The steel's quality directly impacts the structure's strength, durability, and overall performance. Proper material selection ensures compliance with engineering standards, enhances safety, and prolongs the building's lifespan.
This article provides a concise guide to help engineers, architects, and builders choose the most suitable steel for their LSF projects, focusing on key factors like strength, corrosion resistance, and compliance with industry standards.
2- Key Factors in Choosing Steel for LSF
When selecting steel for Light Steel Frame (LSF) structures, several critical factors need to be considered to ensure the structure is safe, durable, and cost-effective. Below are the key factors:
2-1 Strength and Durability
The strength of the steel determines its ability to withstand loads and stresses during construction and throughout the structure's lifespan. Two important properties to evaluate are:
- Tensile Strength: The maximum stress that steel can endure while being stretched or pulled before breaking.
- Yield Strength: The stress level at which steel deforms permanently.
Steel grades such as G550 and G450 are commonly used in LSF structures due to their high strength-to-weight ratio, making them ideal for lightweight yet robust designs.
2-2 Corrosion Resistance
Corrosion can significantly reduce the lifespan of a steel structure. To mitigate this, the following are crucial:
- Galvanized Coatings: Steel coated with zinc (e.g., Z275 or G90) provides excellent corrosion resistance.
- Additional Coatings: Polymeric or paint-based coatings may be used in highly corrosive environments for added protection.
Choosing corrosion-resistant steel ensures the longevity of the LSF structure, especially in humid or coastal regions.
2-3 Thickness and Profile Compatibility
The thickness of the steel plays a vital role in determining its performance in specific applications:
- Structural Adequacy: Thicker steel sections provide better load-bearing capacity but may be harder to work with.
- Assembly and Profile Fit: Ensure that the chosen thickness aligns with the design of the profiles and connections in the structure.
Steel thicknesses typically range from 0.5 mm to 2.0 mm for LSF applications, depending on the intended use.
3- Types of Steel Used in LSF Structures
Selecting the right type of steel is crucial for ensuring the strength, durability, and efficiency of LSF (Light Steel Frame) structures. The following are the most commonly used types of steel:
3-1 High-Strength Steel Grades
- G550 Steel (High Tensile Strength):
G550 steel is a popular choice for LSF structures due to its high tensile strength of 550 MPa. It allows for lighter profiles without compromising structural integrity, making it ideal for cost-efficient designs. - G350 Steel (Balanced Strength and Ductility):
With a tensile strength of 350 MPa, G350 steel is slightly less strong than G550 but offers improved ductility, which can be advantageous for specific applications like curved or more complex profiles.
3-2 Cold-Formed Steel (CFS)
- Definition:
Cold-formed steel is manufactured by bending thin sheets of steel into desired profiles at room temperature. - Advantages:
- Lightweight yet strong, ideal for prefabricated construction.
- Precision in dimensions ensures easy assembly and consistency.
- Excellent compatibility with fasteners like self-drilling screws and rivets.
3-3 Galvanized Steel
- Why Galvanization Matters:
Galvanized steel is coated with a layer of zinc to protect it from corrosion and extend its lifespan, especially in environments prone to moisture or humidity. - Coating Specifications:
- Z275 (275 g/m²): A common coating standard offering excellent corrosion resistance.
- Z350 and above: Higher zinc coatings are used for environments with extreme conditions, like coastal or industrial zones.
3-4 Sustainable Steel Options
- Many manufacturers now offer steel made with recycled materials, aligning with the growing demand for sustainable construction practices.
- These options do not compromise on strength or performance but reduce the environmental footprint.
By understanding these types of steel and their characteristics, engineers and builders can make informed decisions that balance performance, cost, and longevity for their LSF projects.
4- Standards and Certifications for LSF Steel Selection
When selecting steel for LSF structures, adhering to recognized standards and certifications ensures safety, quality, and long-term performance. Below are key aspects to consider:
4-1 International Standards for LSF Steel
Standards define the mechanical properties, chemical composition, and coating requirements for steel used in LSF structures. Some widely recognized standards include:
- ASTM Standards (USA):
- ASTM A653/A653M: Specifies the requirements for zinc-coated (galvanized) steel sheets.
- ASTM A1003/A1003M: Covers the specifications for steel used in cold-formed framing.
- EN Standards (Europe):
- EN 10346: Specifies continuously hot-dip coated steel flat products, including galvanized steel.
- AS/NZS Standards (Australia/New Zealand):
- AS/NZS 4600: Standards for cold-formed steel structures.
4-2 Importance of Certification
Certifications from reputable organizations ensure the steel meets the necessary standards. Look for certifications like:
- ISO 9001: Demonstrates the manufacturer's commitment to quality management.
- CE Marking (Europe): Indicates compliance with European safety and performance requirements.
- UL or ICC-ES (North America): Certifies that the steel has been evaluated for safety and performance.
4-3 Coating and Corrosion Protection
For LSF structures, steel must be protected against corrosion, especially in humid or coastal environments. Common coatings include:
- Galvanization (Zinc Coating): Measured by weight per area (e.g., G90, G60 in ASTM standards).
- Zinc-Aluminum Coatings: Offer enhanced corrosion resistance (e.g., ZAM®, Galvalume®).
4-4 Benefits of Using Standardized Steel
- Ensures consistency and reliability in performance.
- Facilitates compatibility with LSF design software like FrameCAD and Howick.
- Reduces risks associated with inferior or non-compliant materials.
4-5 Tips for Compliance
- Always request material test reports (MTRs) or certificates of compliance from suppliers.
- Verify that the steel’s properties align with design requirements and the specific standards mentioned.
By adhering to these standards and certifications, you can ensure your LSF structures are both safe and durable while maintaining cost-effectiveness.
5- Practical Tips for Steel Selection
When selecting steel for LSF structures, it's essential to focus on both quality and performance. Below are some practical tips to ensure you choose the best material for your project:
5-1 Choose a Reliable Supplier or Manufacturer
- Work with reputable suppliers who provide certified materials.
- Check the supplier's track record, customer reviews, and compliance with standards.
- Request material test certificates (MTC) to verify the steel's properties, including its grade, thickness, and coating.
5-2 Consider Cost vs. Performance
- While budget constraints are important, avoid compromising on quality to save costs.
- Low-cost steel may lack the necessary durability or corrosion resistance, leading to higher maintenance costs and safety risks in the long term.
- Invest in steel with appropriate coatings (e.g., zinc or aluminum-zinc) to enhance longevity, especially in harsh environments.
5-3 Match Steel Properties with Project Requirements
- Ensure the chosen steel grade meets the structural design specifications (e.g., tensile strength and yield strength).
- Consider the thickness and profile compatibility with the assembly process to avoid misfits during construction.
5-4 Verify Compliance with Standards
- Check for compliance with international or local standards such as:
- ASTM (American Society for Testing and Materials).
- EN (European Norms).
- AS/NZS (Australian/New Zealand Standards).
- Materials meeting these standards provide assurance of quality, safety, and performance.
5-5 Factor in Environmental Conditions
- Assess the location and environmental exposure of the structure.
- For coastal or industrial areas, prioritize high corrosion resistance, such as steel with advanced galvanization or coating.
- In seismic regions, choose steel with excellent ductility to ensure structural stability during earthquakes.
By keeping these tips in mind, you can make informed decisions that optimize the performance, safety, and lifespan of your LSF structure.
6- Conclusion
Selecting the right steel for Light Steel Frame (LSF) structures is a critical decision that directly affects the safety, durability, and cost-efficiency of the project. Prioritizing high-quality steel with appropriate strength, corrosion resistance, and compatibility with design requirements ensures a robust and long-lasting structure.
Adhering to international standards and certifications not only guarantees quality but also enhances the structure’s compliance with regulatory requirements. Investing in reliable suppliers and balancing cost with performance are key to achieving optimal results.
Ultimately, the choice of steel should reflect the project’s unique demands while upholding safety and sustainability. By considering the factors discussed in this guide, engineers and builders can make informed decisions and ensure the success of their LSF projects.
7- References
When writing about steel selection for LSF structures, it is essential to provide references to ensure credibility and offer readers additional resources for detailed information. Below are some key references you can include:
- Standards and Specifications:
- ASTM A1003/A1003M: Standard for steel sheet specifications used in cold-formed steel construction.
- AS/NZS 4600: Cold-formed steel structures standard applicable in Australia and New Zealand.
- EN 1993-1-3: European standard for the design of cold-formed steel members.
- AISI S100: North American specification for the design of cold-formed steel structural members.
- Guidelines and Best Practices:
- Light Steel Framing Manual by Steel Framing Alliance: Comprehensive resource for LSF design and material selection.
- Cold-Formed Steel Design (Book by Wei-Wen Yu and Roger A. LaBoube): Authoritative text on the behavior and design of cold-formed steel.
- Manufacturer and Industry Resources:
- Technical datasheets from reputable manufacturers like FrameCAD, Howick, or Dahezb.
- Industry whitepapers and case studies related to LSF projects.
- Research Papers:
- Academic and peer-reviewed journals, such as those found in the Journal of Constructional Steel Research.
- Web Resources:
- Websites like steel.org for up-to-date industry standards.
- Manufacturer-specific online tools and software for LSF design.