Selecting the Correct Screws for Assembling Light Gauge Steel Frame Structures
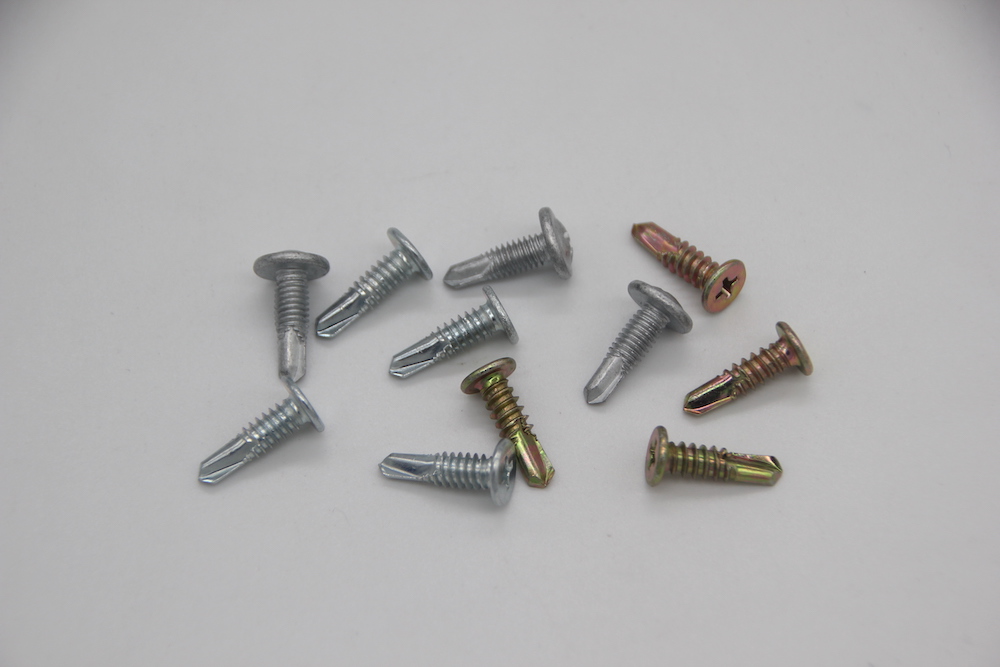
1. Introduction to Light Gauge Steel Frame Structures
Light gauge steel framing (LGSF) represents a modern and increasingly prevalent construction method that utilizes cold-formed steel coils, typically with a thickness of less than ¼ inch, to create the primary structural framework for buildings . This approach stands in contrast to traditional construction materials like wood and concrete, as well as heavier hot-rolled steel sections, offering distinct advantages particularly in terms of weight, ease of handling, and speed of construction . The terms LGSF, steel framing, cold-formed steel (CFS), and various abbreviations thereof (LGS, CFS framing) are often used interchangeably within the construction industry to refer to this versatile technique . The fundamental process involves precisely forming and cutting these thin steel coils into lightweight yet strong structural components, which serve as the skeleton of a building, including elements such as roof trusses, wall studs, and floor joists .
The adoption of LGSF has seen significant growth on a global scale, with widespread use in countries across Europe, Japan, New Zealand, Australia, and the United States, and its popularity is rapidly increasing in regions like India . This widespread acceptance underscores the recognized benefits and expanding application of LGSF in contemporary construction practices. The consistency in terminology, despite the various names used, suggests a maturing understanding and standardization within the industry regarding this construction method. Furthermore, the increasing global adoption indicates that LGSF is a well-established and reliable construction technology, supported by a growing body of knowledge, industry standards, and a diverse range of available products, including the crucial fasteners required for assembly.
2. The Critical Role of Fasteners in LGSF Assembly
The selection of the correct screws is of paramount importance in the assembly of light gauge steel frame structures . These seemingly small components are fundamental to ensuring the overall structural integrity and load-bearing capacity of the entire LGSF system. Proper screw selection directly influences the frame's ability to withstand the intended loads, including dead loads (the weight of the structure itself), live loads (occupants and movable objects), and environmental loads (wind, snow, seismic forces), without experiencing failure . Beyond load-bearing, the correct fasteners are crucial for maintaining the stability and rigidity of the frame, preventing unwanted movement or deformation that could compromise the building's structural performance and the integrity of finishes .
The durability and longevity of an LGSF structure are also significantly influenced by the fasteners used . Strong and lasting connections between the steel members, achieved through appropriate screw selection, contribute to the overall lifespan of the building. Conversely, the use of incorrect fasteners can lead to weakened connections, increasing the risk of structural failure under various stresses . This not only compromises the safety of building occupants but can also result in violations of building codes, leading to potential fines, project delays, and costly rework . Moreover, inappropriate fasteners can lead to increased maintenance costs over time due to loosening or corrosion, ultimately reducing the lifespan of the LGSF structure . Therefore, fasteners in LGSF are not merely incidental hardware; they are integral structural components whose proper selection and installation are essential for the safety and performance of the entire building.
3. Understanding Screw Types for Steel Construction
Various types of screws are utilized in steel construction, each designed for specific applications and materials. Understanding these distinctions is crucial for selecting the appropriate fasteners for LGSF assembly.
-
Machine screws, often referred to as bolts or stove bolts, are primarily employed for joining metal components to each other or for attaching metal to other materials such as hard plastics and wood . These screws are often used in applications where disassembly might be required. Machine screws are available in a wide variety of head types, including pan, button, countersunk, Torx, flat, round, and hex, catering to diverse aesthetic and functional needs . They are typically manufactured from materials like stainless steel for corrosion resistance and zinc-plated steel for general applications . A key characteristic of machine screws is that they are usually fully threaded with a blunt end, designed to be used in conjunction with nuts or tapped holes .
-
Self-drilling screws, commonly known as Tek screws (named after the original brand), are designed to streamline the assembly process by drilling their own pilot hole and forming the mating threads in a single operation . This eliminates the need for pre-drilled holes, making them highly efficient for joining sheet metal or attaching metal to other materials. Self-drilling screws feature a sharp drill point that enables them to penetrate metal with relative ease . They are available in various designs with different lengths to accommodate a range of material thicknesses and are widely used across numerous industries . Furthermore, self-drilling screws are offered with various head types, including bugle, button, countersunk, hex, and pan, to suit different application requirements and desired finishes .
-
Self-tapping screws and sheet metal screws are often used interchangeably to refer to fasteners designed to tap their own threads as they are driven into a material . This thread-forming action can be achieved through a sharp pointed tip, suitable for softer materials, or a flat, blunt tip that typically requires a pilot hole . While specifically manufactured for use in metal-based materials, self-tapping screws can also be used for fastening softer surfaces like wood . Their ability to create their own threads ensures a secure grip in the material .
For the specific application of metal stud framing in LGSF, several specialized screw types are commonly employed:
-
Metal to Metal Connection Screws are designed for joining steel framing members to each other.
- Low profile framing screws are short, self-drilling screws ideal for connecting metal studs in metal stud framing. They feature a low-profile head, such as a modified truss head or a pancake head, which is suitable for applications where the connection will be subsequently covered with materials like plywood or drywall . Common sizes include #10 x 3/4″ Modified Truss Head Self Drilling Screws and 10 x 5/8″ Pancake Framers, which can often be used interchangeably for both interior and exterior load-bearing walls and headers .
- Hex head screws are a robust option for metal-to-metal connections where the surface will not be covered by sheathing, such as in roof and floor truss assemblies . These screws, typically available in #12 and #14 gauges and various lengths, offer excellent grip and are easy to drive .
-
Wall Covering to Metal Connection Screws are used to attach various sheathing materials to the metal frame.
- Self-drilling drywall screws are designed for connecting gypsum board to structural metal studs that are 20 gauge or thicker . These screws are typically zinc-coated, feature a Phillips drive, and have a flat head. Many also have a bugle-shaped head that allows them to countersink into the drywall paper without tearing it .
- Sharp point drywall screws are used for attaching gypsum board to lighter gauge metal studs, typically 20 gauge EQ and thinner . Like self-drilling drywall screws, they have a flat head and Phillips drive, and phosphate-coated options are also available .
- Sheathing screws are specifically designed for connecting plywood, OSB, and other structural boards to metal studs . These screws often have an unthreaded section near the head to prevent the sheathing from being pulled away from the stud. They are commonly #6 in size, zinc-coated, and utilize a #1 square drive for secure fastening .
-
General Utility Screws serve various fastening needs beyond the primary structural connections and sheathing.
- Trim screws are used for attaching wood trim to either drywall or structural metal studs . They typically have a trim head, which is small and often countersunk, to provide a clean and less visible finish.
- Long bugle head screws are useful for attaching wider materials, such as 2x lumber, to metal studs . These screws can be up to 4″ long, with a common size being #8 x 2 5/8″.
- Long modified truss head screws are similar to long bugle head screws and are also used for attaching wide materials like lumber or lathe to metal studs . They are often available in #8 gauge with lengths of 1 5/8″ and 2 1/2″.
-
Structural Fasteners represent a broader category encompassing fasteners used in primary structural applications.
- Heavy hex bolts are characterized by their large, thick hexagonal head and are ideal for high-strength steel-to-steel structural connections, commonly used in bridge and building construction .
- Construction screws include a wide range of specialized fasteners such as self-drilling screws, roofing screws, reamer screws, and lath screws, each designed for specific structural fastening tasks .
The categorization of screw types based on their specific application within LGSF underscores the specialized nature of fasteners used in this construction method. Selecting the correct screw for each connection type is crucial for ensuring the structural integrity and safety of the LGSF structure. The prevalence of self-drilling screws in LGSF highlights the industry's focus on efficiency and speed, as these screws eliminate the need for pre-drilling in many metal-to-metal connections.
Screw Type | Common Applications in LGSF | Head Type | Point Type | Drive Type | Typical Size Range |
Low Profile Framing Screw | Metal stud to stud connections where sheathing will be applied | Modified Truss, Pancake | Self-Drilling | Phillips (#2) | #10 x 3/4", 10 x 5/8" |
Hex Head Screw | Metal to metal connections not being sheathed (trusses) | Hex | Self-Drilling | Hex | #12, #14 (various lengths) |
Self-Drilling Drywall Screw | Gypsum to structural metal studs (20 ga+) | Bugle, Flat | Self-Drilling | Phillips (#2) | #6 (various lengths) |
Sharp Point Drywall Screw | Gypsum to lighter gauge metal (20 ga EQ and thinner) | Bugle, Flat | Sharp | Phillips (#2) | #6 (various lengths) |
Sheathing Screw | Plywood/OSB to metal studs | Flat | Sharp | Square (#1) | #8 (various lengths) |
Trim Screw | Wood trim to metal studs | Trim | Sharp | Square (#1), Phillips (#2) | #6 (various lengths) |
Long Bugle Head Screw | Lumber to metal studs | Bugle | Self-Drilling | Phillips (#2) | #8 (up to 4") |
Long Modified Truss Head Screw | Lumber or lathe to metal studs | Modified Truss | Self-Drilling | Phillips (#2) | #8 (1 5/8", 2 1/2") |
4. Specific Screw Recommendations for LGSF Assembly
For connecting structural members in LGSF, such as studs, tracks, joists, and trusses, the choice of screw depends on whether light gauge steel is being connected to light gauge steel or to heavier gauge steel. Self-drilling screws are generally recommended for efficient fastening in both scenarios, eliminating the need for pre-drilling and saving valuable time and labor .
When joining light gauge steel members to other light gauge steel members, for instance, when attaching studs to track in lighter gauge (e.g., 20-25 gauge) applications, sharp point pan framing screws like the #7 x 7/16″ size with a #2 Phillips drive can provide a suitable and cost-effective solution . For stud-to-stud connections, particularly in areas that will be covered by sheathing materials like plywood or drywall, low profile framing screws such as the #10 x 3/4″ Modified Truss Head Self Drilling Screw or the 10 x 5/8″ Pancake Framer are often preferred to ensure a flush surface . These screws typically utilize a #2 Phillips head. The use of fine thread screws can also be advantageous when engaging with the thin steel material of light gauge framing, as they tend to provide a more secure grip without causing damage . Some manufacturers have even developed combined thread designs that incorporate both fine and coarse threads to cater specifically to the unique demands of light gauge steel framing . Additionally, modified truss head screws, often in the #8 gauge, offer a larger load-bearing surface compared to standard pan head screws, which can be beneficial in certain connections requiring increased pull-through resistance .
In situations where light gauge steel needs to be fastened to heavier gauge steel members, self-drilling screws with a drill point (often referred to as a Tek point) specifically designed for the thickness of the heavier gauge steel are necessary to ensure proper penetration . Common sizes for such applications include #12 and #14 gauge screws with varying drill point numbers (e.g., #3, #4, #5), with the appropriate number depending on the specific thickness of the steel being drilled. Pan framer screws equipped with drill points that are engineered for penetrating heavier steel tracks to connect to light gauge steel studs are also a viable option, with drill point sizes ranging from #1 to #6 available to suit different connection requirements .
When it comes to attaching sheathing materials to the light gauge steel frame, different types of screws are recommended based on the material being fastened. For attaching drywall to metal studs (typically in the 20-25 gauge range), fine thread drywall screws in the #6 gauge with a bugle head and a #2 Phillips drive are specifically designed to countersink into the drywall surface without tearing the paper . The length of these screws should be chosen based on the number of drywall layers being installed and the thickness of the steel studs. In cases where thicker gauge steel studs are used, self-drilling drywall screws, also in #6 gauge, are recommended to ensure efficient penetration through the steel . For lighter gauge steel studs (20 gauge EQ and thinner), sharp point fine thread screws in #6 gauge with a bugle head and a #2 Phillips drive are often sufficient for attaching drywall .
For attaching plywood, OSB, and similar structural boards to light gauge steel studs, sheathing screws, typically in the #8 gauge with a zinc coating and a #1 square drive or a combo drive head, are well-suited . The presence of an unthreaded shank on these screws helps to pull the sheathing tight against the framing members. Self-drilling wafer-head screws with wings are also particularly useful for this application, as the wings are designed to create a clearance hole in the sheathing as the screw is driven, preventing the screw from binding or breaking when it engages the steel stud .
For fastening other components and accessories, such as trim and lath, to the LGSF structure, specific screw types are recommended. For attaching wood trim to metal studs, trim screws, often in the #6 gauge with a trim head and a #1 square drive or #2 Phillips drive, provide a clean and less visible finish . The appropriate length should be selected based on the thickness of the trim material. When attaching metal lath and stucco mesh to steel studs (typically in the 20-25 gauge range), modified truss sharp screws, often in the #8 gauge, are recommended due to their holding power and ability to lay flat against the mesh .
The guidelines provided by manufacturers of LGSF systems often include very specific recommendations regarding the types, sizes, and installation techniques for screws to be used with their particular products and components. Adhering to these manufacturer recommendations is of critical importance for ensuring the structural integrity and maintaining the warranty of the LGSF system. Different LGSF systems may have unique connection details and load transfer mechanisms that necessitate the use of specific fasteners to ensure proper performance. Furthermore, the gauge of the light gauge steel members being used in the framing directly influences the selection of the appropriate screw point type, whether it be sharp, self-piercing, or self-drilling, as well as the required screw gauge and length to achieve adequate penetration and secure holding power. Using the correct screw based on the steel gauge is essential to avoid issues such as stripping or inadequate fastening.
5. Material Composition and Corrosion Protection of LGSF Screws
The material composition of screws used in LGSF assembly plays a significant role in their strength, durability, and resistance to corrosion. Common screw materials include carbon steel and stainless steel, each with its own advantages and considerations . While carbon steel offers a good balance of strength and cost-effectiveness, making it a common choice for many construction applications, including LGSF, its inherent susceptibility to rust necessitates the application of protective coatings, particularly in environments where moisture is present . Medium carbon steel, containing between 0.3% and 0.6% carbon, is often preferred for screw manufacturing due to its optimal combination of strength and ductility .
Stainless steel, on the other hand, is an alloy that contains a minimum of 10.5% chromium, which naturally forms a protective layer of chromium oxide on the surface of the metal . This passive layer provides excellent resistance to corrosion, making stainless steel screws a preferred choice, especially in outdoor and marine environments where rust is a significant concern. Various grades of stainless steel, such as 304, 316, and 410, offer different levels of corrosion resistance and strength characteristics, allowing for selection based on the specific application requirements . For instance, Grade 316 exhibits superior resistance to chloride ions, making it suitable for coastal regions, while Grade 410 offers higher strength but lower corrosion resistance compared to the 300 series stainless steels .
In addition to the base material, the corrosion protection of screws is of paramount importance in LGSF due to the potential for both interior and exterior applications . Corrosion can weaken the connections between LGSF members, ultimately compromising the structural stability and safety of the building . Several common protective coatings are used to enhance the corrosion resistance of steel screws. Zinc coating, or galvanization, is a widely used and relatively inexpensive method that involves applying a layer of zinc to the steel surface . Hot-dip galvanization (HDG) results in a thicker zinc layer, providing superior corrosion resistance ideal for outdoor and coastal environments . Electrogalvanization (EG), or zinc plating, applies a thinner layer of zinc and is suitable for less severe environments . Zinc alloy coatings, such as zinc-aluminum, also offer enhanced protection . Phosphate coating provides a moderate level of corrosion resistance and also improves the adhesion of paints . Ceramic coatings are engineered to resist salt water spray, making them suitable for marine applications . Other coatings like nickel plating, chrome plating, and zinc flake coating are also used for specific purposes .
When selecting screw materials and coatings for LGSF, several factors should be taken into consideration. The severity of the environmental conditions to which the structure will be exposed is a primary concern . The potential for galvanic corrosion between dissimilar metals in the assembly should also be evaluated . Finally, the project budget and the desired lifespan of the structure will influence the choice, as more corrosion-resistant options often come with a higher cost. The decision between using carbon steel with a protective coating and opting for stainless steel will depend on the specific environmental context and the long-term performance requirements of the LGSF structure. Stainless steel offers inherent and superior corrosion resistance but typically at a higher initial cost. Different levels of galvanization, such as G40, G60, and G90, indicate the thickness of the zinc coating and the level of corrosion protection provided, with higher numbers signifying greater resistance, particularly important in regions with aggressive environmental conditions as mandated by local building codes . Therefore, careful consideration of the material composition and corrosion protection of LGSF screws is a critical aspect of ensuring the long-term durability and structural integrity of the building.
6. Relevant Building Codes and Industry Standards for Fasteners in LGSF
Adherence to relevant building codes and industry standards is crucial for ensuring the safety and structural integrity of light gauge steel frame structures. Several key codes and standards provide guidance and requirements for the use of fasteners in LGSF.
The International Building Code (IBC) serves as a primary reference for commercial and many residential building projects, containing provisions relevant to steel framing and often referencing industry standards for specific requirements . For residential construction, the International Residential Code (IRC) provides specific guidelines, including a prescriptive method for cold-formed steel framing and detailed requirements for fasteners used in steel-to-steel connections and for attaching sheathing materials . Notably, the IRC specifies minimum screw edge distances and center-to-center spacing for steel-to-steel connections, requiring self-drilling tapping screws that conform to ASTM C1513 . For attaching structural sheathing, the IRC mandates minimum No. 8 self-drilling tapping screws also conforming to ASTM C1513, with specific head diameter and installation requirements . When attaching gypsum board, the IRC requires minimum No. 6 screws conforming to either ASTM C954 or ASTM C1513 . A fundamental requirement across these connections is that screws must extend through the steel by at least three exposed threads . It is also essential to be aware of local building codes, which may have additional or more stringent requirements beyond the model codes .
Several key industry standards are also relevant. AISI S100, the North American Specification for the Design of Cold-Formed Steel Structural Members, is referenced by the IBC and provides the primary design criteria for LGSF . ASTM C1513, the Standard Specification for Steel Tapping Screws for Cold-Formed Steel Framing Connections, is referenced by both the IRC and IBC, setting performance requirements for these critical fasteners . ASTM C954 specifies requirements for drill screws used with gypsum board . ASTM A653/A653M details the requirements for zinc and zinc-iron alloy coatings on steel sheets used in framing . ASTM C645 provides specifications for nonstructural steel framing members, including screw spin-out performance tests , while ASTM C955 covers load-bearing steel studs and tracks . In regions like Australia and New Zealand, standards such as AS/NZS 4600 and AS 3566 are relevant, as referenced by manufacturers like MiTek .
Compliance with these building codes and industry standards is not only a legal obligation but also fundamental to ensuring the safety and structural integrity of LGSF buildings. Adhering to these regulations facilitates the permitting and approval processes and helps to avoid potential liabilities. The explicit references to specific ASTM standards within the IRC and IBC emphasize the importance of using screws that have been tested and certified to meet these rigorous performance criteria for LGSF connections. Similarly, the existence of regional standards highlights the need to be aware of and comply with the specific regulations applicable to the project's geographic location.
7. Manufacturer Guidelines and Best Practices for Screw Selection
Leading manufacturers of LGSF systems and fasteners, such as Grabber, Simpson Strong-Tie, MiTek, JZ Fastener, and Fong Prean, offer valuable guidelines and recommendations for selecting the appropriate screws for assembling their products.
Grabber provides a wide array of steel framing screws with features like precision-designed recesses, premium pan heads, and under-head serrations for secure fastening in light-gauge framing . Their screws often feature a sharp Vector Point™ for faster driving and are engineered to resist hydrogen embrittlement. Grabber offers detailed specifications on various screw attributes, aiding in proper selection .
Simpson Strong-Tie offers a range of metal screws specifically designed for cold-formed steel framing and sheathing attachment, including self-drilling options with different head types and drill point sizes . They also provide collated screw options for increased installation speed using their Quik Drive® systems .
MiTek, in their steel framing guide for the Australian and New Zealand markets, recommends using specific gauge Tek screws (10 and 12 gauge) that comply with AS 3566 Class 3 corrosion resistance for their connectors, based on calculations following AS/NZS 4600-2005 . They specify allowable screw head types and sizes based on steel grade and thickness .
JZ Fastener specializes in screws designed for light gauge steel framing, emphasizing features like finer threads, thinner heads, enhanced corrosion resistance, and sufficient load-bearing capacity . They offer various screw types, including dual thread designs for improved grip.
Fong Prean recommends self-drilling screws for heavy-gauge steel and sharp-point framing screws for light-gauge steel, highlighting the importance of proper screw selection for structural integrity and installation efficiency .
General best practices for screw selection in LGSF include using self-drilling screws for efficient metal-to-metal connections, especially in thicker steel, and selecting sharp point screws for thinner gauge steel to ensure quick penetration . Ensuring the screw length is appropriate for the total thickness of the materials being joined, with at least three threads extending beyond the steel, is also crucial . Using the correct drive bit to prevent stripping and avoiding overdriving screws are essential installation practices . For large projects, using collated screws with auto-feed screw guns can significantly improve efficiency .
The specific features and benefits emphasized by different manufacturers indicate that the optimal screw choice can depend on the specific LGSF system and project requirements. Therefore, it is advisable for users to research and compare offerings from various manufacturers based on their particular needs. The consistent advice to avoid overdriving screws highlights a common installation error that can compromise the integrity of the connection, underscoring that proper installation technique is as important as selecting the correct screw.
8. Key Factors to Consider When Choosing Screws for LGSF
Selecting the appropriate screws for light gauge steel frame structures requires careful consideration of several key factors that directly impact the performance and durability of the assembly.
The gauge and thickness of the steel members being joined are primary determinants in screw selection . Heavier gauge, thicker steel generally necessitates the use of self-drilling screws with a more aggressive drill point to effectively penetrate the material without the need for pre-drilling. The drill point number on self-drilling screws indicates their drilling capacity through specific steel thicknesses. Conversely, for lighter gauge, thinner steel, sharp point or self-piercing screws may be sufficient and can offer a faster installation process. The gauge (diameter) of the screw should also be considered in relation to the steel thickness to ensure adequate holding power.
The type of materials being connected is another critical factor . Steel-to-steel connections within the LGSF structure require specialized metal framing screws, often self-drilling, for a strong and lasting joint. When attaching sheathing materials like drywall or plywood to the steel frame, screws with specific head types (bugle for drywall, wafer for plywood) and thread types (fine thread for metal) optimized for these material combinations should be used. If the design involves connecting wood components to the LGSF, specialized wood-to-steel screws with appropriate thread patterns and point types are necessary.
The load-bearing requirements of the connection dictate the necessary strength of the screws . Structural connections in load-bearing walls, floors, and roofs require screws with sufficient shear and tensile strength to withstand the anticipated forces. Heavier loads may necessitate larger diameter screws or a greater number of fasteners to distribute the load effectively. Consulting engineering specifications is crucial for connections with significant load requirements.
Environmental conditions and the potential for corrosion must be carefully evaluated . For LGSF structures in exterior environments or areas with high humidity, salt spray, or chemical exposure, using corrosion-resistant screws made from stainless steel or coated carbon steel is essential. When fastening dissimilar metals, the risk of galvanic corrosion should be considered, and compatible screw materials should be selected.
The head type, drive style, and point type of the screw are also important considerations . The head type should be chosen based on the application and desired finish. The drive style should match the available tools and offer good resistance to stripping. The point type should be appropriate for the thickness and type of material being fastened.
Finally, the screw length and diameter (gauge) must be appropriate for the specific application . The length should accommodate the thickness of all mater
Factor | Implications for Screw Selection | Relevant Screw Characteristics |
Steel Gauge & Thickness | Determines drilling capacity needed | Point Type (Sharp, Self-Piercing, Self-Drilling), Drill Point Number, Gauge |
Materials Being Connected | Requires material-specific screw designs | Screw Type (Metal Framing, Drywall, Sheathing, Wood-to-Steel), Head Type, Thread Type |
Load-Bearing Requirements | Demands sufficient strength and holding power | Gauge, Length, Material (High-Strength Steel), Number of Fasteners |
Environmental Conditions | Necessitates corrosion resistance | Material (Stainless Steel), Coating (Galvanization, Ceramic) |
Head Type | Affects finish and tool compatibility | Bugle, Pan, Hex, Wafer, Trim |
Drive Style | Influences ease of use and stripping resistance | Phillips, Square, Hex, Torx |
Point Type | Determines drilling/penetration capability | Sharp, Self-Piercing, Self-Drilling (Tek) |
Screw Length | Ensures adequate material penetration and thread engagement | Length (based on total material thickness + 3 exposed threads) |
Screw Diameter (Gauge) | Impacts strength and holding power | Gauge (related to load requirements and steel thickness) |
9. Conclusion and Expert Recommendations
In conclusion, selecting the correct screws for assembling light gauge steel frame structures is a multifaceted process requiring careful consideration of numerous factors. These factors include the gauge and thickness of the steel members, the specific materials being connected, the load-bearing demands of the connections, the environmental conditions and potential for corrosion, the head type, drive style, and point type of the screws, and the appropriate screw length and diameter.
Based on the analysis of the research material, the following recommendations are provided:
- Always consult project-specific structural drawings, relevant building codes (including IBC, IRC, and local amendments), and the guidelines provided by the manufacturers of the LGSF system being used.
- Ensure that the screw type and point style are appropriately matched to the gauge and thickness of the steel members being joined.
- Select screw types and head styles that are specifically designed for the materials being connected (e.g., metal framing screws for steel-to-steel, drywall screws for gypsum board).
- Choose screws with sufficient strength and load-bearing capacity for the intended structural application.
- Prioritize the selection of corrosion-resistant screws, either stainless steel or coated carbon steel, based on the anticipated environmental exposure.
- Verify that the selected screw length is adequate to pass through all connected materials and provides the minimum required thread engagement in the receiving steel member.
- Employ proper installation techniques and the correct tools to avoid common issues such as overdriving or stripping the screws.
By meticulously considering these factors and adhering to best practices in screw selection and installation, construction professionals can ensure the assembly of robust, durable, and safe light gauge steel frame structures that comply with all relevant standards and provide reliable long-term performance.